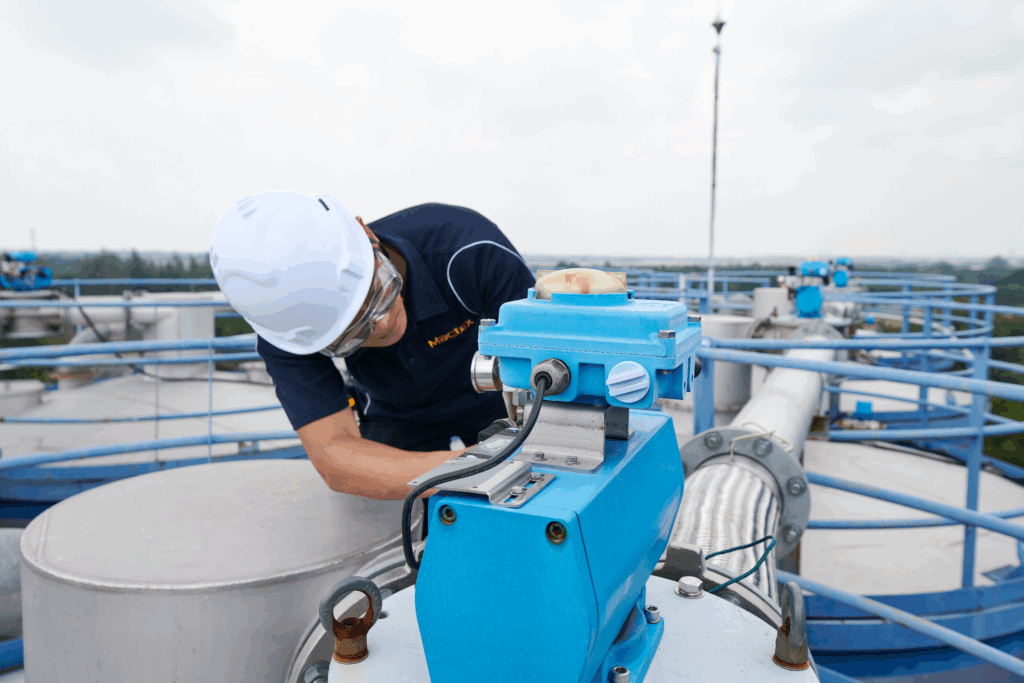
Pneumatic conveyors are vital systems in industries such as Food and Beverage (F&B), Petrochemical, Oleochemical, and Minerals and Ceramics.
These systems use air pressure to transport bulk materials — such as powders, granules, and pellets — through enclosed pipelines, offering a safe, efficient, and contamination-free method of material handling. Their ability to move large volumes of material quickly makes them indispensable in production lines where speed and reliability are paramount.
However, the intense operational demands placed on pneumatic conveyors, including high pressures, abrasive materials, and near-constant use, subject them to significant wear and tear.
Without proper attention, this wear can lead to reduced efficiency, unexpected breakdowns, and costly repairs.
This is why regular conveyor servicing is essential. By implementing consistent maintenance, businesses can greatly extend the longevity of their pneumatic conveyors, ensuring they operate at peak performance while avoiding the disruptions and expenses tied to system failures.
In addition to delivering top-notch pneumatic conveying solutions, MACTEX specialises in delivering tailored maintenance services that address the specific needs of these systems, helping industries maintain productivity and protect their investments.
Telltale maintenance issues and how scheduled maintenance can help
Pneumatic conveyors operate in challenging conditions that accelerate deterioration. Some of the most common issues that arise due to wear and tear include:
- Pipeline blockages: Over time, materials like fine powders or sticky granules can accumulate inside pipelines, obstructing airflow and reducing the system’s ability to transport materials efficiently. If not addressed, blockages can halt operations entirely.
- Seal degradation: Seals and gaskets, which maintain the system’s air-tight integrity, wear out under constant pressure and exposure to abrasive materials. This leads to air leaks, lowering system pressure and efficiency.
- Component wear: Key parts such as valves, pumps, and filters experience gradual degradation. For example, a worn valve may fail to regulate airflow properly, while a clogged filter can strain the system and increase energy consumption.
Ignoring these problems can have serious consequences. A minor issue, such as a small leak, might seem inconsequential at first, but over time, it can escalate into a major failure that requires extensive repairs or even a full system replacement.
In industries like Petrochemicals, where production downtime can cost thousands of dollars per hour, such failures are particularly detrimental.
Regular conveyor servicing acts as a preventive measure, identifying and resolving these issues before they become critical, thereby preserving the system’s functionality and extending its lifespan.
For example, consider a Minerals and Ceramics facility where abrasive dust is transported daily. Without routine checks, dust buildup could erode pipeline interiors, leading to breaches that compromise the system. Proactive maintenance catches such problems early, saving both time and money.
Click here to learn more about the technological intricacies behind pneumatic conveying systems and how they work.
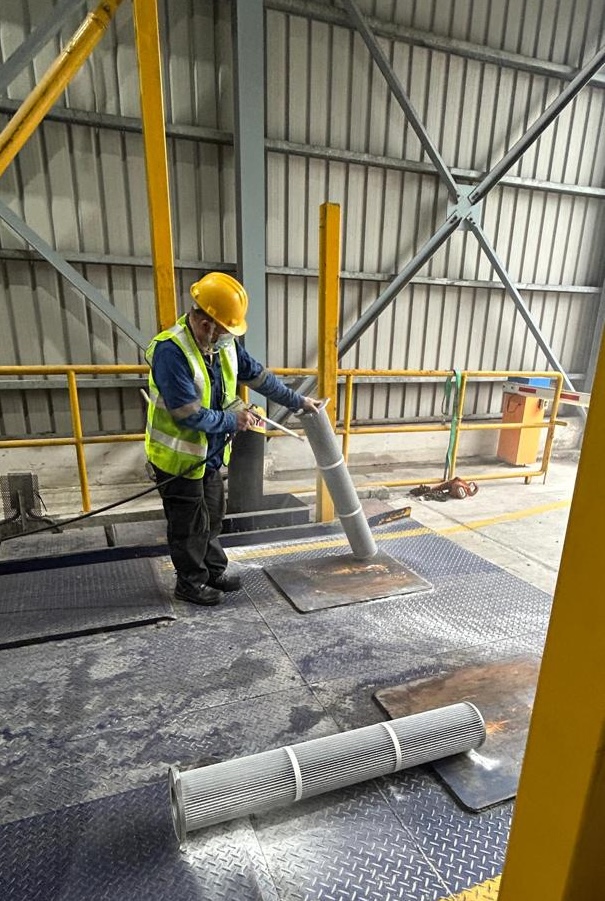
Essential maintenance practices to employ for your company
To ensure pneumatic conveyors remain reliable and efficient, several best practices should be followed:
- Thorough and effective cleaning: Regular cleaning prevents material buildup that could clog pipelines or damage components. Cleaning methods like air purging or flushing with inert gases are effective, especially in the Food and Beverage industry, where hygiene is non-negotiable. Clean systems also reduce the risk of cross-contamination between batches.
- Lubrication: Moving parts such as valves, pumps, and bearings require consistent lubrication to minimize friction. This not only reduces wear and tear but also enhances operational efficiency by ensuring smooth performance.
- Routine inspections: Scheduled inspections allow technicians to spot early warning signs, such as unusual noises, pressure drops, or worn gaskets. Early intervention prevents minor issues from escalating into major repairs, maintaining system integrity.
- Component replacement: Replacing parts like filters, seals, and hoses before they fail is a proactive step that avoids unexpected downtime. For instance, swapping out a filter that’s nearing the end of its life can prevent airflow restrictions that strain the entire system.
These scheduled maintenance practices form a comprehensive maintenance strategy that keeps pneumatic conveyors in top condition.
MACTEX can help businesses avoid the pitfalls of reactive maintenance (where repairs are only made after a failure occurs) by helping them adopt a proactive approach.
Other advantages of consistent conveyor servicing
The benefits of regular servicing and employing best practices go far beyond simply avoiding breakdowns. Here’s how it pays off:
- Extended longevity: Routine care protects critical components from excessive wear, allowing conveyors to operate effectively for years longer than neglected systems. In industries like Minerals and Ceramics, where replacing heavy-duty equipment is a major expense, this extended lifespan is a significant advantage.
- Enhanced reliability: A well-maintained conveyor is far less likely to fail unexpectedly, ensuring consistent production schedules. This reliability is invaluable in sectors like Petrochemicals, where even brief interruptions can disrupt supply chains and incur hefty losses.
- Cost efficiency: While maintenance involves upfront costs, it’s a fraction of the expense tied to emergency repairs or premature system replacements. Additionally, efficient conveyors consume less energy and reduce material waste, offering long-term savings. In the Food and Beverage industry, for instance, preventing spoilage due to system delays can save thousands annually.
- Improved safety: Regular checks and good cleaning methods ensure compliance with safety standards, minimizing risks like pressure leaks or material spills. This is critical when handling hazardous substances in Oleochemical plants or maintaining hygiene in food production.
These advantages make regular servicing a smart investment, delivering both immediate operational improvements and long-term financial benefits.
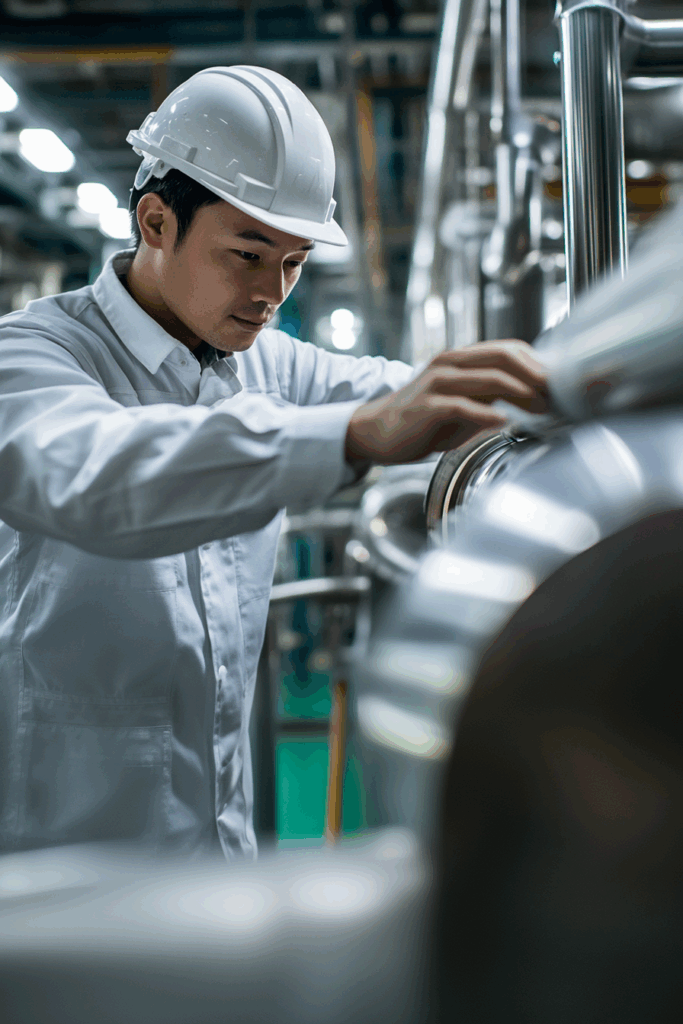
Safeguard your workflow with MACTEX’s maintenance expertise
MACTEX brings unparalleled expertise to pneumatic conveyor maintenance, offering services designed to meet the diverse needs of our clients.
Our offerings include:
- Preventive maintenance programmes: These include regular inspections, effective cleaning, lubrication, and component assessments to keep systems running smoothly and prevent issues before they occur.
- Customised conveyor servicing plans: We understand that every industry and operation is unique. MACTEX tailors maintenance schedules to your specific materials, production demands, and budget, ensuring maximum efficiency without disrupting your workflow.
- Expert support: Our experienced technicians have a deep understanding of pneumatic conveying systems across industries, delivering high-quality care backed by years of hands-on expertise.
Our results speak for themselves. For example, a Food and Beverage client saw a 40% reduction in pipeline clogs after implementing our custom, effective cleaning routines.
Similarly, a Mineral processing facility cut annual repair costs by 25% through our proactive component replacement approach. These case studies highlight how MACTEX’s solutions translate into measurable improvements in performance and long-term savings.
Next steps: Secure the longevity of your systems
More than just things to check off on a list, regular servicing and scheduled maintenance are strategic moves that can ensure the longevity, reliability, and efficiency of your pneumatic conveyors.
Partnering with MACTEX gives you access to expert care that safeguards your equipment and boosts your bottom line.