When it comes to material handling, waste represents a significant issue, with approximately 9.2 billion tonnes of industrial waste produced annually. This is true across a wide range of industries.
In F&B, waste often arises from perishable goods like flour or liquids, where spillage or contamination compromises safety and escalates costs. In Petrochemicals, hazardous material losses can lead to environmental risks and regulatory penalties.
Meanwhile, in Minerals and Ceramics, abrasive materials like clay or sand contribute to cleanup expenses and resource depletion, impacting both profitability and sustainability.
From spillage and overuse to inefficient processes, material waste not only drives up operational costs but also harms the environment. Factors such as manual handling errors, outdated equipment, and poor system design often contribute to these high waste levels.
For businesses aiming for sustainable logistics and cost efficiency, reducing waste has become a top priority.
Fortunately, advancements in automation and pneumatic systems offer a path towards zero-waste operations. When integrated properly, these technologies can help businesses streamline material handling, minimise losses, and move closer towards achieving their sustainability goals.
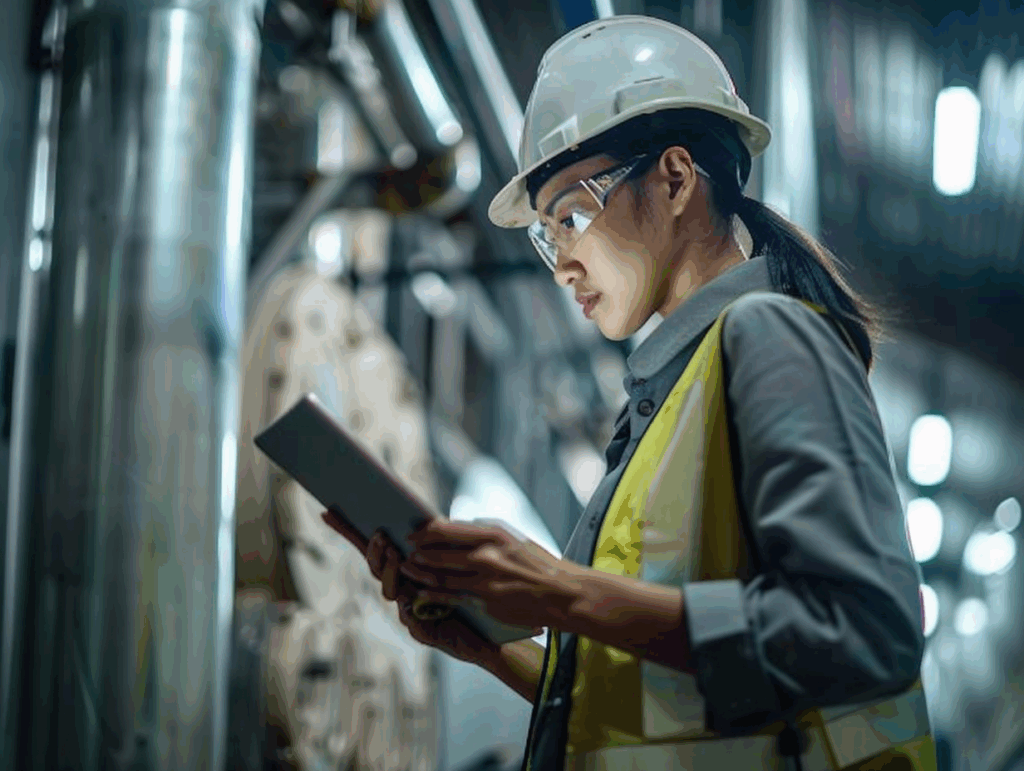
Explaining automation in material handling and how it works with pneumatic systems.
At its core, automation in material handling refers to the use of technology to control and optimise the movement, storage, and processing of materials within minimal human intervention.
This can include pneumatic conveying systems, debagging systems, or sensors that monitor material flow.
When coupled with pneumatic systems (which use air to transport materials through enclosed pipelines), automation becomes a powerful tool for reducing waste and boosting efficiency.
Automated pneumatic systems leverage sensors and control units to monitor material flow in real time, adjusting air pressure to prevent blockages or overuse. Integration with Industry 4.0 technologies, like IoT, enables predictive maintenance, reducing downtime and ensuring seamless operation.
Pneumatic systems are great at moving bulk materials like powders and granules with precision. Unlike traditional mechanical conveyors, they minimise spillage and contamination by keeping materials fully contained.
When automated, these systems can adjust flow rates, detect blockages, and optimise transfer speeds in real time. This synergy delivers efficiency through automation, ensuring materials reach their destination without excess loss or overuse.
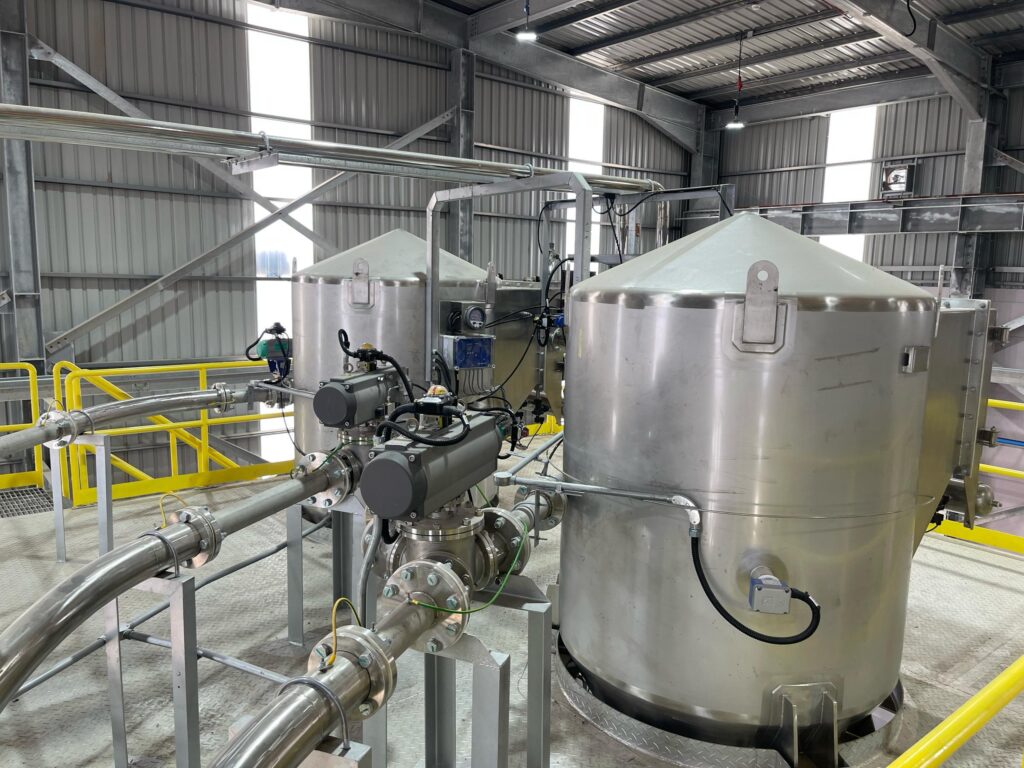
Why pneumatic systems are so effective at reducing waste
When it comes to waste-reduction, pneumatic systems lead the pack due to their enclosed design. Problems such as leaks and spills (which are common with open conveyors) are greatly reduced, while the addition of automation goes even further in tackling these issues.
For instance, sensors can detect and adjust operating pressure accordingly, ensuring no excess is used. This level of accuracy is critical in industries such as Oleochemicals, where over-handling can degrade sensitive materials.
MACTEX’s systems are engineered with these challenges in mind. Their custom designs minimise downtimes, reduce energy consumption, and eliminate inefficiencies that lead to waste. In a nutshell, MACTEX-designed systems provide businesses with a way to account for every gram of material used, down to the finest margins.
Learn how MACTEX’s pneumatic conveying systems can help improve material handling processes and overall throughput.
Reducing waste and increasing efficiency with MACTEX’s expertise
For businesses seeking to enhance efficiency, MACTEX stands out with its tailored turnkey solutions.
Advanced pneumatic systems integrate seamlessly with automation capabilities, offering features like real-time monitoring and adaptive controls.
These feature custom-engineered pipelines and adaptive airflow controls, tailored to each client’s material type — whether powders, liquids, or granules. Additionally, modular designs allow easy scalability and maintenance, cutting long-term costs and reinforcing their leadership in waste-reducing solutions.
These integrations not only reduce material waste, but also cut operational costs and improve environmental sustainability.
By minimising spillage and ensuring precise handling, systems built by MACTEX can help businesses achieve their zero-waste goals while consistently maintaining high throughput – a win-win for profitability and the environment.
The benefits of combining automation and pneumatic systems go beyond waste reduction. Let’s take a look at how these technologies can deliver tangible results:
- Reduced Material Waste:
Automated pneumatic conveyor systems ensure exact amounts of material are transported, eliminating overuse. For example, in the F&B industry, precise handling of flour or sugar can prevent costly losses. Data shows that automation can generally reduce material waste and improve food safety in bulk handling processes. - Cost Savings:
By reducing waste, and optimising workflows, businesses see significant savings. Automation eliminates the inefficiencies of manual labour, while pneumatic systems lower maintenance costs compared to traditional conveyors prone to wear and tear. - Environmental Sustainability:
Less waste translates to a smaller environmental footprint. MACTEX’s solutions support sustainable logistics by cutting down on resource depletion and landfill contributions, which aligns with the world’s sustainability trends.
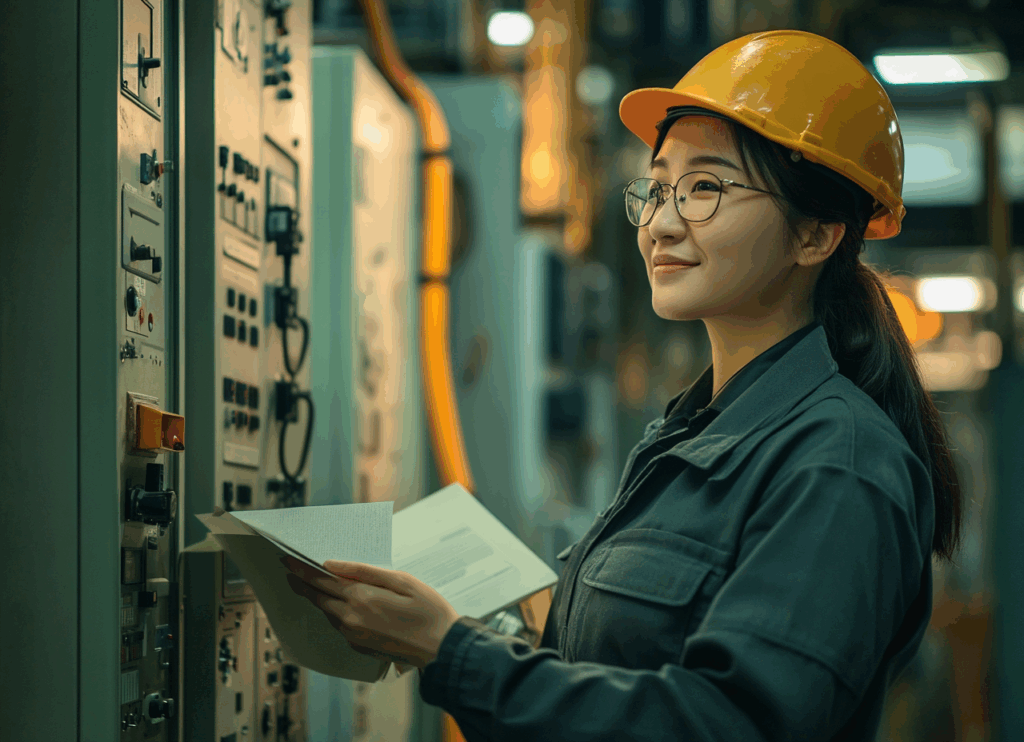
When it comes to improving efficiency all round, MACTEX’s record speaks for itself.
In the Petrochemical sector, MACTEX implemented an automated pneumatic system for a client handling fine powders, which resulted in a significant reduction in material waste and a marked increase in throughput within six months.
In the Mineral and Ceramics industry, an automated system designed by MACTEX considerably reduced spillage during clay transport, saving the client thousands in annual cleanup costs.
These examples, among others, highlight how reducing material waste through automation can transform operations across a diverse range of industries.
Partner with MACTEX to ensure your business becomes more cost-effective, efficient, and sustainable.
With the global push for zero-waste growing stronger each day, transforming yours to adapt is no longer optional, but a necessary competitive edge.
Automation efficiency paired with pneumatic systems offers a proven way to reduce material waste, lower costs, and embrace sustainable logistics.
For businesses looking to gain an edge, MACTEX can be trusted to bring decades of expertise to the table, delivering advanced systems that meet unique demands across numerous industries.
During a consultation, MACTEX’s team evaluates your setup, identifies waste-reduction opportunities, and designs a tailored solution. Post-installation, their ongoing support ensures sustained efficiency and sustainability.