Conveyor systems in modern manufacturing
In modern manufacturing and material handling, there are two primary conveyor systems used across industries — pneumatic conveyors and mechanical conveyors.
Both industrial material handling systems come with advantages and disadvantages, making them suitable for different applications and industry preferences.
Choosing the right conveyor system is crucial for efficiency, productivity, reliability, and cost-effectiveness. Nevertheless, there are many things to consider before making a decision on the right material handling system, including conveyor system costs, energy consumption, and material handling suitability.
MACTEX Sdn Bhd specialises in solid bulk material handling, offering end-to-end and customised turnkey solutions for various modern manufacturing needs. Serving a breadth of clients from different industries, MACTEX Sdn Bhd is an expert in designing and installing material handling solutions, while also supplying conveyor system components.
Reach out to MACTEX Sdn Bhd to find out more about how their conveyor systems can help optimise the material handling process.
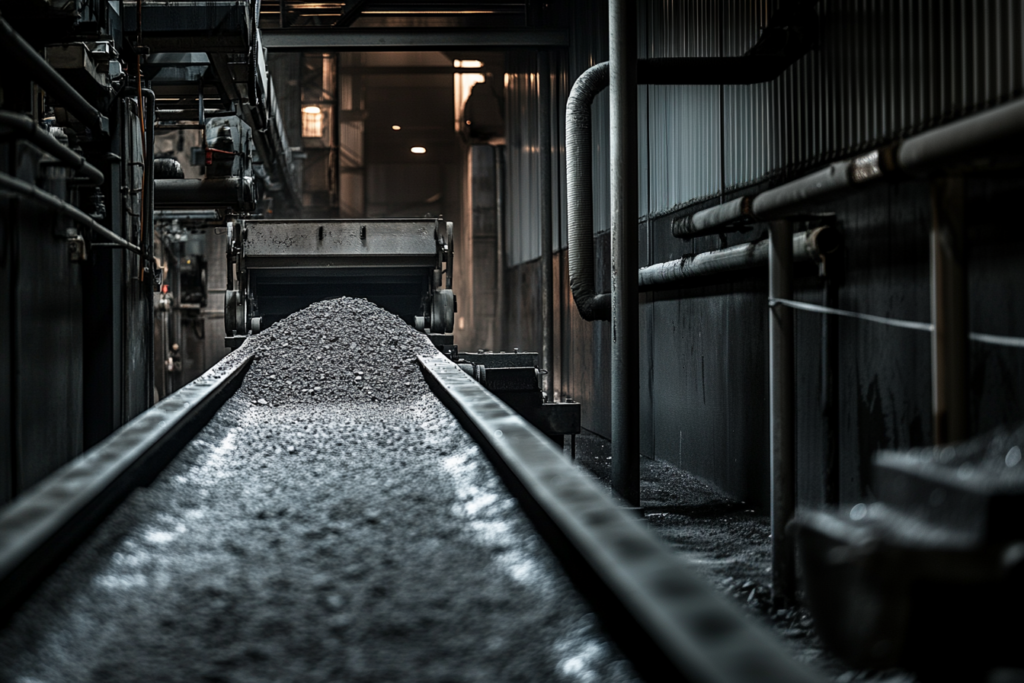
Overview of mechanical conveyor systems
Mechanical conveyor machines use mechanical force to move material from one location to another. They are commonly used in mining, construction, and food processing.
Mechanical conveying relies on physical components to transport material, typically heavy, bulky goods like minerals, construction materials, and large industrial products. It is also the preferred system for materials with high moisture, fat, or oil content, like cake mix, titanium dioxide, and brown sugar.
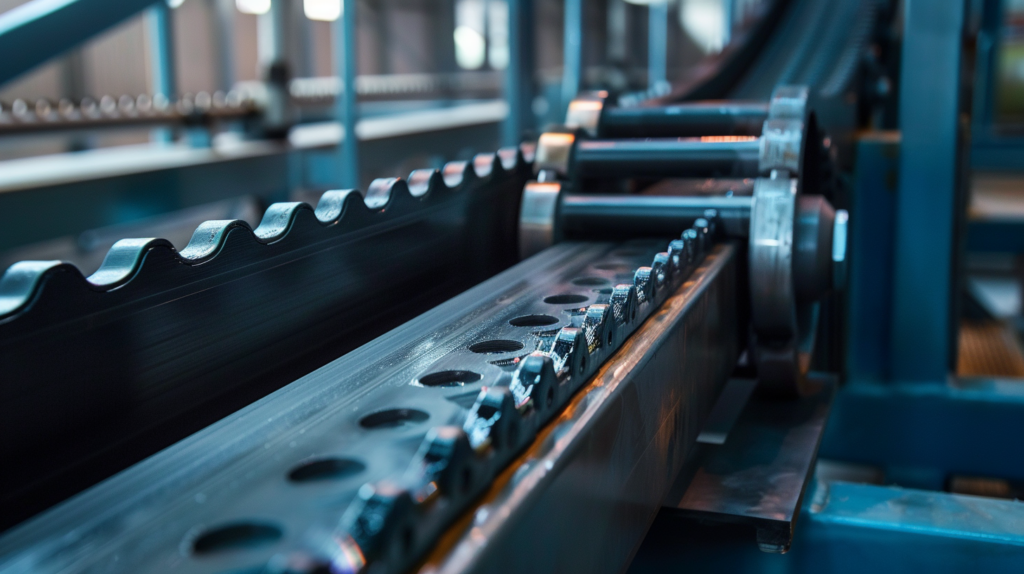
Components of mechanical conveyor machines include belt conveyors, bucket elevators, screw conveyors, vibrating conveyors, drag chain conveyors, driver motors, and rollers.
Belt conveyors, for instance, utilise a continuous band to move materials horizontally or on an incline. Bucket elevators are used to elevate products to high positions. Vibrating feeders, on the other hand, use vibrating trays to transfer moist products without clumping or sticking.
In a mechanical conveying system, a motor will supply energy to the conveyor machine, allowing materials to be moved efficiently. Since most mechanical conveying systems are open, they are less suitable for air-sensitive materials.
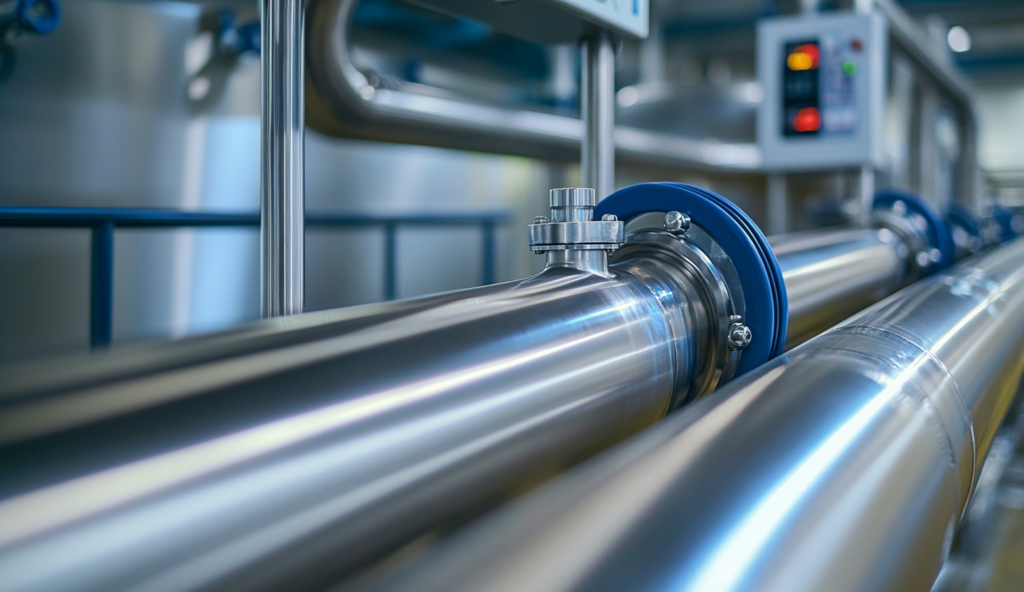
Overview of pneumatic conveyor systems
Pneumatic conveyor machines use air flow to transport bulk material like powders, granules, and small particles through enclosed pipelines.
In pneumatic conveyor machines, air flow is usually generated by a vacuum or pressure system using components like vacuum pumps, blowers, and compressors. Other common components include long bends, rotary valves, double flaps, and venturis.
Unlike mechanical conveying systems, pneumatic conveying lines are more flexible, can travel longer distances, and can accommodate diverse materials with minimal manual handling. This is why pneumatic conveyor machines are favoured in industries like pharmaceuticals, chemicals, and food processing.
There are two subcategories of pneumatic converting: dense phase systems and dilute phase systems.
Dilute Phase Conveying Systems
For dilute phase conveying, materials travel at high speeds while being suspended in air within pipelines. It is suitable for light, non-abrasive, and non-fragile materials ranging from powders to granules. A dilute phase conveyor costs less and is not as complex to build as its dense phase counterpart.
Dense Phase Conveying Systems
Dense phase conveying transports material more slowly, in a slug-like form, through pipelines. It is suitable for heavier, abrasive, and fragile materials ranging from seeds to sand. A dense phase conveyor costs more to build and travels shorter distances.
Learn more about different pneumatic conveyor systems and their ideal applications in modern manufacturing by contacting MACTEX Sdn Bhd.
Comparing the efficiency and operational costs of pneumatic and mechanical systems
In terms of energy consumption, mechanical conveyors are usually more energy efficient compared to pneumatic conveyors, which need significant power to generate air flow. Nevertheless, pneumatic conveyors have come a long way and can achieve comparable energy consumption levels thanks to advanced compressor technology and system design.
When it comes to pneumatic and mechanical conveyor system costs, it is important to look into the initial setup cost, energy costs, and operational costs.
A pneumatic conveyor system costs more to set up initially, and may also incur higher energy costs. However, well-designed pneumatic conveying systems have fewer moving parts, are easier to maintain, and can be automated for efficiency.
A mechanical conveyor system costs more operationally, due to wear and tear on physical components. More frequent maintenance can also lead to downtime, which decreases operational continuity.
Comparing the suitability and scalability of pneumatic and mechanical systems
The suitability of material handling depends on the type of material, distance to be conveyed, and required throughput.
Fragile materials are suited for pneumatic systems, as enclosed pipelines ensure minimal material degradation, maintain product integrity, and reduce dust generation. Pneumatic conveyors are also better suited for longer distances and higher throughput.
On the other hand, mechanical conveyors are suitable for abrasive materials that are required to travel shorter distances.
In certain cases, both types of conveyor machines can be used, and it is up to the operator to weigh the pros and cons of each system.
Looking at the long-term scalability of pneumatic and mechanical conveying systems, the former is favoured for its flexibility in routing and ease of installation into complex layouts. Mechanical conveying systems, however, provide scalability for high load capacities and heavy materials, as long as space and layout are not an issue.
Industry-specific conveyor system recommendations:
F&B: Pneumatic conveyors are often preferred for their cleanliness and ability to handle delicate products ranging from flour and spices, to grains and beans.
Pharmaceuticals: Enclosed pipelines of pneumatic conveyor machines make them ideal for handling sensitive materials like fine chemical powders and tablet granules.
Construction and mining: Mechanical conveyors are better suited for heavy-duty demands, such as transporting gravel, sand, and ores across rugged sites.
Manufacturing: Both pneumatic and mechanical systems can be used, depending on the specific requirements. For instance, cement production often utilises mechanical conveyors to move heavy, raw materials like limestone. Within the same facility, pneumatic conveyors may also be used for finer materials like cement powder.
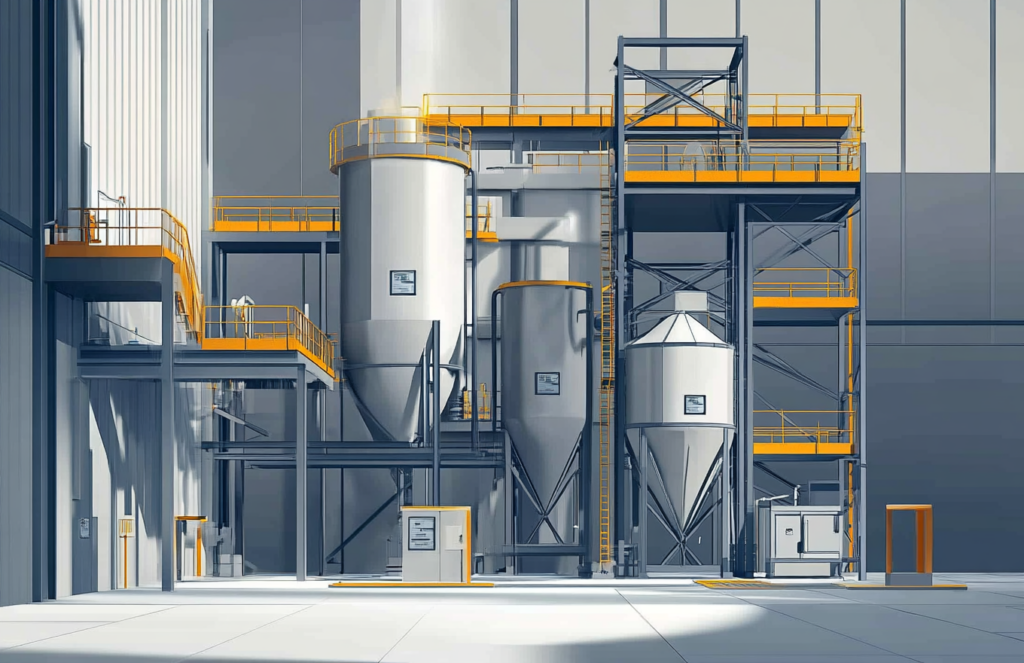
How to choose the right conveyor system
Ultimately, there are many factors to consider when choosing the right kind of industrial material handling system, including conveyor system cost, operational efficiency, energy consumption, material suitability, and long-term scalability.
While mechanical conveyors are equipped for heavy duty material handling, pneumatic conveyors are designed to provide flexibility and reliability across a diverse range of bulk material.
Looking to make an informed decision with professional assistance? Consult with an expert from MACTEX Sdn Bhd to find the best way to optimise the material handling process.
Get a tailored solution for every modern manufacturing need!